Machines used in Yarn Manufacturing:
- Cotton Harvester: Machine for harvesting cotton bolls. Mechanical cotton harvesters are of two basic types, strippers and pickers.
Input: Cotton Plant
Output: Cotton Fiber
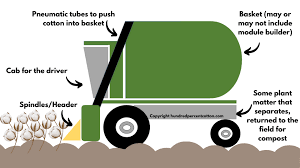
Fig: Cotton Harvester Machine
- Automatic Bale Opener (UNIfloc A-12): The automatic bale opener UNIfloc A 12, featuring advanced bale take-off technology, contributes significantly to cost-effective operations in the blowroom.
Input: Cotton Bale
Output: Lap/Chute feed
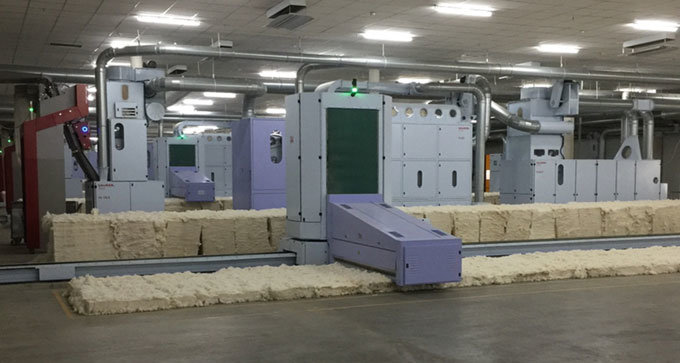
Fig: Automatic bale opener
- Uniclean B12: The pre-cleaner UNIclean B12 is fed with microtufts from the UNIfloc A 12. The tufts are fine-cleaned in the UNImix and UNIstore cleaning modules. In the UNIclean B 12, double hooks pick up the material and mechanically pass it over the cleaning grid five times. The raw material is then directed across the integrated dedusting surfaces. The finest seed coat fragments and dust are mechanically removed.
Input: Cotton Lap
Output: Clean Fiber
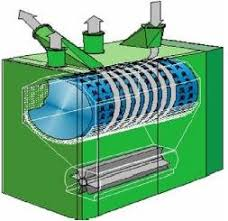
Fig: Uniclean B12
- Unimix: The Unimix machine is used in the blow room. The Unimix is designed to blend different types of fibers. It plays an important role in the early stages of yarn production, where raw fibers are processed and prepared before they can be spun into yarn. The fibers are mixed and opened up in a large chamber, which helps to remove impurities and improve the yarn’s quality.
Input: Clean fiber
Output: Mixed of different grades of fiber
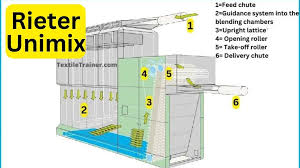
Fig: Unimix
- Unistore (Unistore A79): The UNIstore A 79 is fed from the upstream machine via a dust extractor or condenser. The material enters the UNIstore storage module first. This module forms a material store (buffer) and feeds the S or R module.
Input: Mixed Fiber
Output: Fiber store for chute feed machine
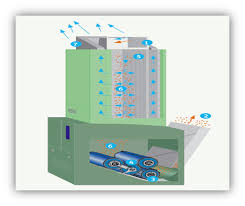
Fig: Unistore A79
- Chute feed machine: Chute feed in carding is a system of feeding small tufts of cotton fibers directly from a blow room to a series of cards, arranged in a circuit through the pneumatic pipe. A condenser in the pneumatic pipe sucks the material from the blow room and delivers it to the flock feeder through the pneumatic pipe by way of the filling trunk.
Input: Cotton fiber
Output: Chute form
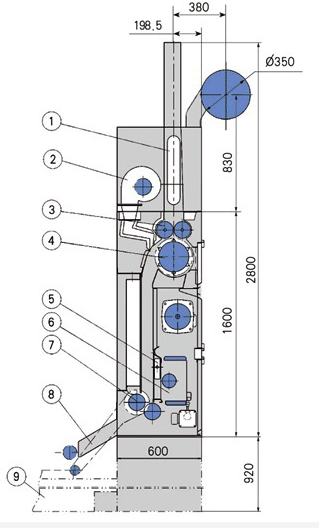
Fig: Chute feed machine
- Carding Machine: Carding is an automated form of payment fraud in which fraudsters test a bulk list of credit or debit card data against a merchant’s payment processing system to verify breached or stolen card details.
Input: Chute feed
Output: Carded sliver
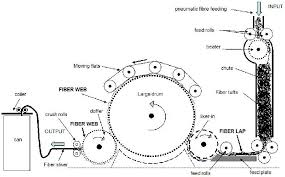
Fig: Carding Machine
- Draw Frame: The basic purpose of the draw frame passages is to obtain a uniform and well-blended sliver through the doubling action at the draw frame and, by the drafting action, to parallelize and straighten fibers, particularly those with hooked ends – whether leading, trailing or both ends.
Input: Carded sliver
Output: Drawn sliver
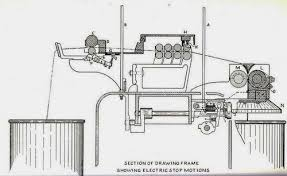
Fig: Drawing Machine
- Combing Machine: Combing is a method for preparing carded fiber for spinning. Combing aligns fibers in parallel before spinning to produce a smoother, stronger, and more lustrous yarn. The basic operations in a combing machine are:
1. Feeding the uncombed sliver into the comb
2. Holding the fibers and combing the free end by pin treatment; any fibers that are not held
will be combed away (the noil)
3. Holding the portion that has just been combed, and repeating the combing operation on the previously uncombed fibers, again removing noil
4. Forming an endless sliver of combed fibers from the tufts that have just been combed.
Input: Carded sliver
Output: Combed sliver
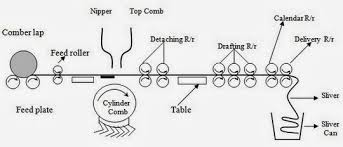
Fig: Combing Machine
- Simplex/Roving Machine: Simplex is an intermediate machine that is used between the draw frame and the ring frame. It is also called a speed frame or roving frame. The main purpose of this machine is to produce the roving package for the ring frame. simplex is called a necessary evil because The first reason is to insert the required draft into a sliver. A drawn sliver is a thick and untwisted strand of fiber that needs a 300~500 draft to be changed to yarn. But yet there is no machine to impart such a great amount of draft to the sliver.
Input: Combed sliver
Output: Roving yarn
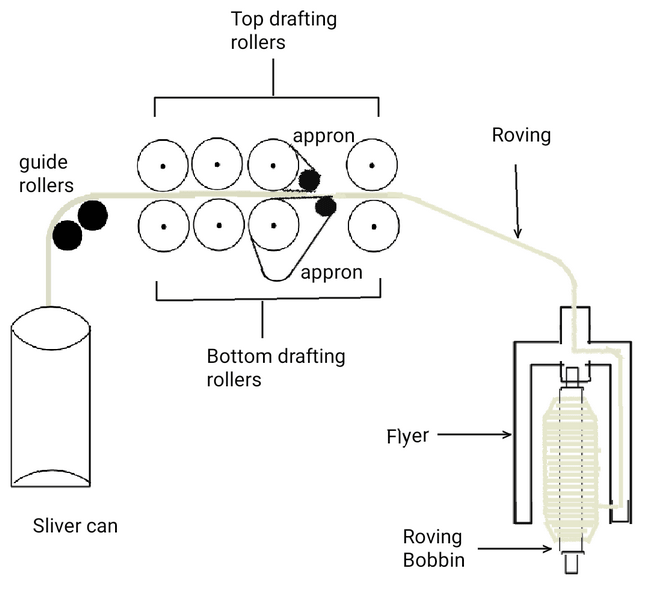
Fig: Simplex Machine
- Ring frame: In spinning, a ring frame is a machine that converts roving into yarn. The main components of ring frame machines are creel – drafting zone – spindle – ring – traveler; it has certain numbers of spindles per machine, and each spindle is a production center.
Input: Roving
Output: Yarn
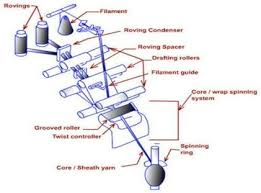
Fig: Ring spinning Machine
- Cone winding: The cone winding machine is a high-level new-generation textile machinery product integrating machines, electricity, instruments, and gas. The tube yarn is wound into a knotless bobbin and the yarn defect is removed during the winding process.
Input: Yarn
Output: Cone
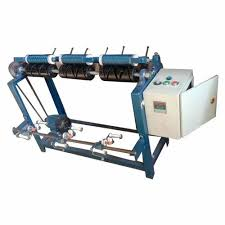
Fig: Cone Winding Machine
- Breaker carding: This machine is used for the carding of jute fiber. This carding machine is used for Removing heavy waste from jute fiber.
Input: Jute fiber
Output: Carded sliver
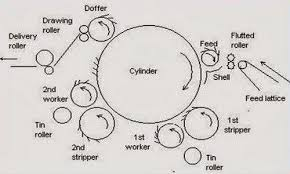
Fig: Breaker card machine
- Finisher carding: This machine is used for the carding of jute fiber. This carding machine removes heavy dust and other waste from jute fiber.
Input: Carded sliver
Output: Carded sliver
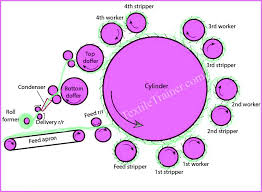
Fig: Finisher Card Machine
- Jute 1st drawing machine(Push bar type): The Jute 1st draw frame machine is used to individualize jute fibers, straighten the fibers, make the fibers in slivers more or less parallel to one another, reduce sliver weight per unit length, increase the uniformity of sliver, Minimization of irregularity by doubling.
Input: Carded sliver
Output: Drawn sliver
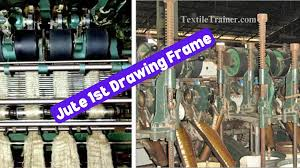
Fig: Jute 1st draw frame
- Jute 2nd & 3rd drawing machine: The process of drawing is used to reduce the width and thickness of slivers by mixing 4 to 6 slivers simultaneously.
Input: Carded sliver
Output: Drawn sliver
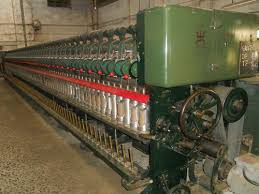
Fig: Jute 3rd draw frame
Machine used in Fabric Manufacturing:
- Machine for weaving:
- Warping machine: A warp machine is used in the textile industry to prepare the longitudinal threads (warp) for threading. The warp machine is responsible for winding the yarn onto a warp beam, sizing the yarn, and arranging the threads in the proper configuration for use on a loom.
Input: Cone on creels
Output: Warp beam
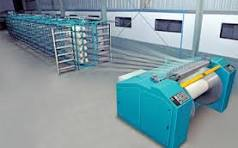
Fig: warping machine
- Sizing machine: This machine is used to size fabrics and is not required for knitting. It is employed in the textile industry to strengthen yarn’s breaking strength and shield it from abrasion.
Input: Warp beam
Output: Sized yarm
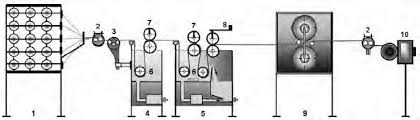
Fig: sizing machine
- Pirn winding machine: A pirn winding machine is a type of textile machinery used to wind yarn onto pirns, which are small, narrow bobbins used in the production of fabrics such as denim, canvas, and twill.
Input: Cone
Output: Pirn
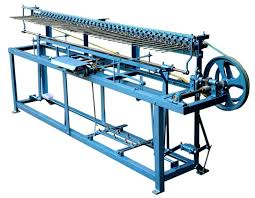
Fig: Pirn winding machine
- Hand loom: A ‘handloom’ is a loom that is used to weave cloth without the use of any electricity. Hand weaving is done on pit looms or frame looms generally located in weavers’ homes. Weaving is primarily the interlacing of two sets of yarn – the warp (length) and the weft (width).
Input: Warp and weft yarn
Output: Woven fabric
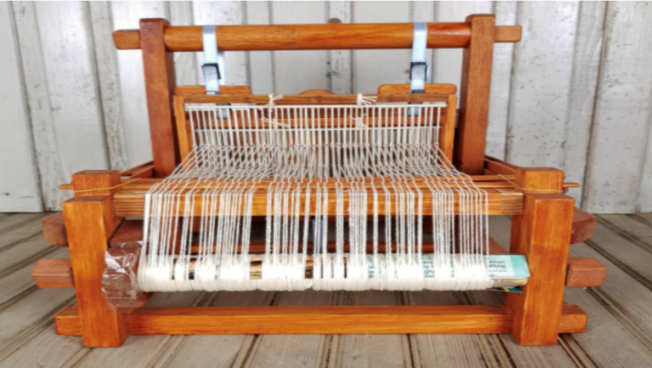
Fig: Handloom
- Frame Loom: A frame loom is the most basic of all weaving looms used by weavers to create woven designs. Historically frame looms were smaller, portable looms made of wood, resembling a picture frame, and originally designed to produce tapestry-style woven designs with a dense and rug-like appearance.
Input: Warp and weft yarn
Output: Woven fabric
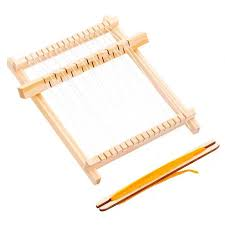
Fig: Frame loom
- Projectile Loom: A projectile loom is a type of shuttleless weaving machine used in the textile industry to produce woven fabrics. Unlike traditional shuttle looms, projectile looms eliminate the need for a shuttle to carry the weft yarn across the warp threads. Popular Widths: Commonly used widths include 190 cm and 330 cm.
Input: Warp and weft yarn
Output: Woven fabric
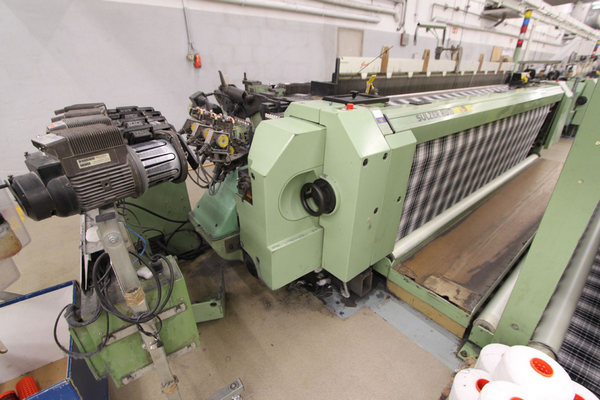
Fig: Projectile Loom
- Rapier Loom: A rapier loom is a shuttleless weaving loom in which the filling yarn is carried through the shed of warp yarns to the other side of the loom by finger-like carriers called rapiers. A stationary yarn package is used to supply the weft yarns in the rapier machine.
Input: Warp and weft yarn
Output: Woven fabric
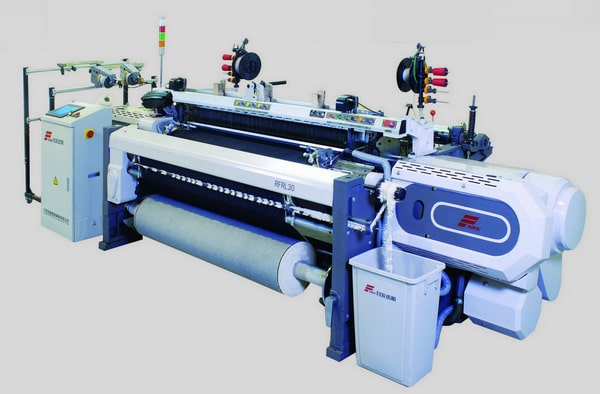
Fig: Rapier Loom
- Air Jet Loom: An air jet loom is described as a shuttle-less loom. It is a type of air jet weaving machine in which a jet of air is typically used by an air jet loom to propel the filling yarn through the weaving shed.
Input: Warp and weft yarn
Output: Woven fabric
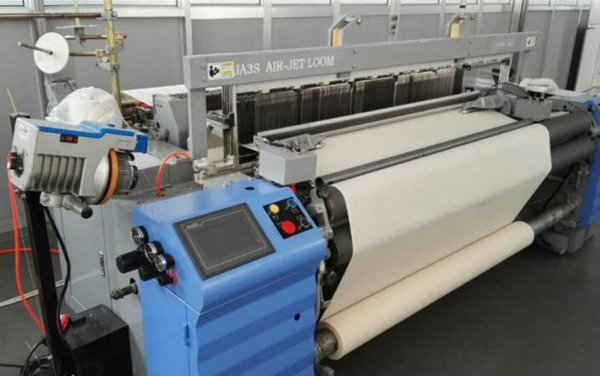
Fig: Air jet Loom
- Water Jet Loom: A water jet loom is similar to an air jet loom but uses water instead of air to transport the yarn around the shed. A water jet loom inserts the filling yarn with highly pressurized water. The tractive force is provided by the relative velocity between the filling yarn and the water jet.
Input: Warp and weft yarn
Output: Woven fabric
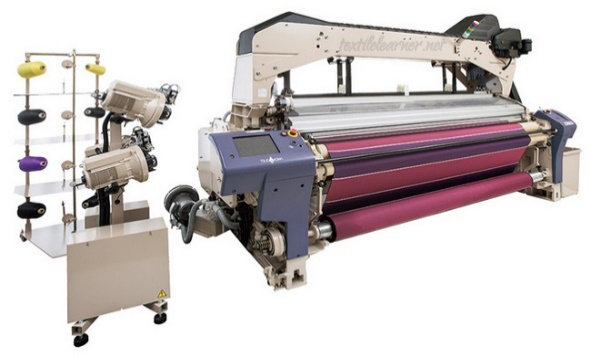
Fig: Water Jet loom
- Multiphase Loom: The phase number of a loom is defined as the average number of shuttles or weft carriers inserting weft simultaneously. It is shown that existing multi-phase looms must have high phase numbers to compensate for their low shuttle velocity.
Input: Warp and weft yarn
Output: Woven fabric
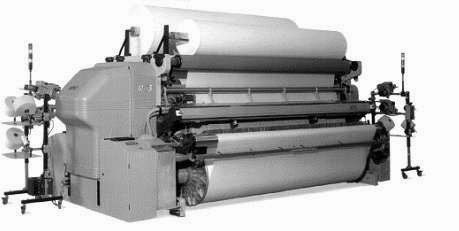
Fig: Multiphase Loom
- Mechanical Jacquard: At the heart of the Jacquard loom is the Jacquard mechanism, a device consisting of punched cards or a punched paper roll. Each card or hole in the paper represents a specific pattern or design element. These cards are attached to a series of needles or hooks that correspond to the warp threads.
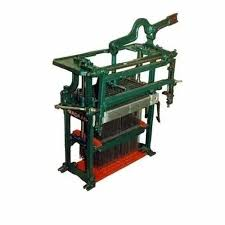
Fig: Mechanical Jacquard
- Electronic Jacquard: The major concept of the electronic jacquard is the warp side is controlled by electro-mechanical hooks. These hooks are controlled by an electronic processing unit called a See-co board. The main advantage of the electronic jacquard is the elimination of the cylinder, a needless cardboard design card.
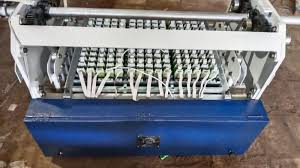
Fig: Electronic Jacquard
- Dobby Loom: A dobby loom, or dobby loom, is a type of floor loom that controls all the warp threads using a dobby device. A loom from the 1890s with a dobby head. Dobbies can produce more complex fabric designs than tappet looms but are limited compared to Jacquard looms.

Fig: Dobby Loom
Machine used for knitting:
- Flatbed Knitting Machine: Flatbed purls or links-links machines are mainly employed to knit some specialty items using double-hooked latch needles. The one set of needles is transferred to knit in either of two directly opposed needle beds using a set of sliders in each bed.
Input: Cone/cheese package
Output: Knit fabric

Fig: Flatbed Knitting Machine
- Circular Knitting Machine: Circular knitting machines always produce a tube-shaped fabric. They exist in different sizes or diameters, depending on the field of application. The needles and sinkers in these machines are arranged in a circle.
Input: Cone/cheese package
Output: Knit fabric
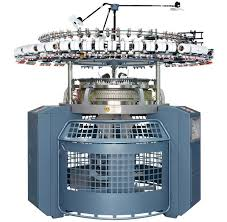
Fig: Circular Knitting Machine
- Raschel knitting machine: Raschel knits do not stretch significantly and are often bulky; consequently, they are often used as an unlined material for coats, jackets, straight skirts, and dresses.
Input: Cone/Cheese package
Output: Knit fabric

Fig: Raschel knitting machine
- Tricot knitting machine: Warp knitting m/c is one kind of flatbed m/c. This m/c produces the knitted loops in Wales direction. Tricot fabric is a type of knitted fabric created using a warp knitting process. The tricot weave creates a zigzag pattern. Synthetic fibers are typically used in this fabric, making it elastic.
Input: Cone/Cheese package
Output: Knit fabric
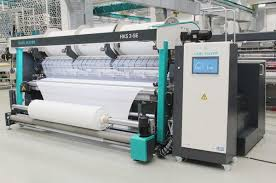
Fig: Tricot knitting machine
- Socks Knitting Machine: Sock knitting machines are highly specialized circular knitting machines specific to the products made on them. These machines can use any type of yarn or fiber to produce hosiery and socks made of shape, size, and performance criteria.
Input: Cone/Cheese package
Output: Socks
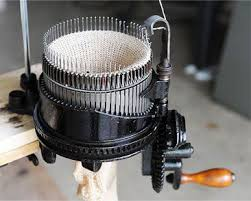
Fig: Socks Knitting Machine
- Double needle bar knitting machine: Double needle bar raschel machines are used for producing three-dimensional textiles. Depending on your requirements, our machines can produce spacer textiles having thicknesses from 1 mm up to approximately 65 mm. This technology is also suitable for producing seamless warp knits and fine lingerie fabrics.
Input: Cone/Cheese package
Output: Knit fabric
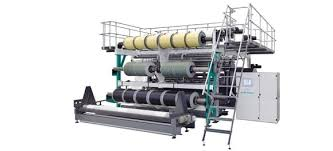
Fig: Double needle bar knitting machine
- Tricot Warp knitting machine: Sinker and Sinker bar: In the tricot warp knitting m/c tricot sinker is used to hold down the loops produced by the needles. The sinker bar keeps the sinkers together to move in unison while knitting. The main function of the sinker is to hold down, knock over, and support the fabric loops.
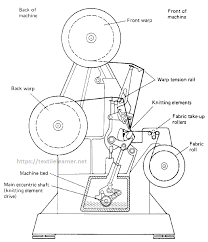
Fig: Tricot warp knitting machine
- Raschel Warp knitting machine: Warp-knitted space fabrics are manufactured using the double needle bed raschel machine. The machine possesses at least four guide bars, but between five and seven guide bars are used most of the time. The Raschel machine could work at higher speeds than the Leavers machine and proved the most adaptable to the new synthetic fibers, such as nylon and polyester.
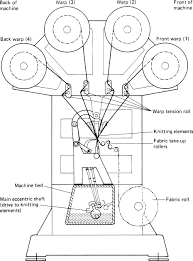
Fig: Raschel Warp knitting machine
- Flat lock knitting machine: A wide range of yarn counts may be knitted per yarn in one knitting system, with the possibility of changing the machine gauge. 3. The operation and supervision of the machine of simple type is relatively less arduous than other Weft Knitting machines. The flat knitting machines can transfer loops from one needle to another needle with an appreciable effect on the knit structure.
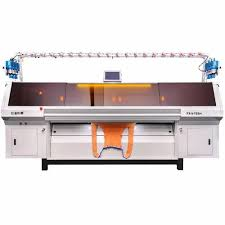
Fig: Flatlock knitting machine
- Lock Stitch Knitting Machine: A single needle lockstitch sewing machine forms lock stitches with one needle thread and one bobbin thread. The needle penetrates the fabric from the top and brings the needle thread through the fabric to the bottom to form a stitch. It is the most common mechanical stitch that can be made by a sewing machine.
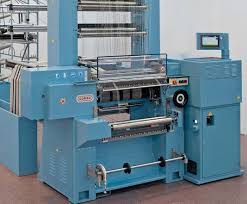
Fig: Lock Stich Knitting Machine
Writer Information
Md Abrar sadman Arpon
Leader, Content Writing Team
Textile Engineers Society
Department of Textile Engineering, JUST